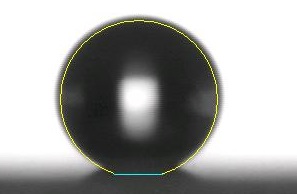
Hydrophobic, self cleaning coatings
An amazing advance in coatings technology is the new superhydrophobic coatings that exhibit self cleaning properties. Super Hydrophobicity is expressed in contact angle values that demontrate how well is a water drop in contact with a solid surface. Different methodologies exist on turning a hydro phillic surface into a super hydrophobic one but all of them depend on two properties; surface roughness and surface free energy. As the surface energy is lowered, surfaces are turned into hydrophobic ones. Such minimization of energies can occur either by structural changes [for example introduction of surface roughness] or chemical ones [chlorination of surface or other chemical modifications].
Such hydrophobic coatings are numerous up to date. Most of them are polymeric matrices with surface modifications, or chemical modifications, or additional curing, or even hybrid coatings. Applications are also numerous and they include self cleaning cars, water resistant glasses, electronics protection, housing insulation and so more. These coatings, among all other advantages, lead to a high decrease of energy and materials required for maintenance of surfaces, and cleaning of surfaces. Toyota has launched a self cleaning model in 2014.
Applications of high interest include glass surfaces, whether these surfaces are located at water tanks, aircrafts, automobiles or house installations. Numerous approaches have been suggested in order to reach hydrophobic, self cleaning formulations and manufacturing/ application pathways:
> One method is based on the creation and deposition of ZnO nanorods on glass surfaces. ZnO nanorods creation occurs via a standard hydrothermal procedure. The ZnO seed layer (about 30 nm) is prepared by radio frequency magnetron sputtering with a ZnO target, at 150W and 20 sccm flow of Ar for 9 min. After seed layer preparation, ZnO nanorod arrays are synthesized at 90 °C, by zinc nitrate hexahydrate (Zn(NO3)2•6H2O, 25 mM), hexamethylenetetramine (25 mM), and deionized water (100 ml). Diameter of the nanorods ranges between 60 and 400 nm, depending on the growth conditions. The two geometric features of ZnO NR [NanoRods] play a significant role for hydrophobicity; for the same length, a greater diameter increases hydrophobicity; for the same diameter, a greater length also increases hydrophobicity. Both occur due to the air trapped in the voids created in the nanostructure. However, the described structure is still hydrophilic. To create a super-hydrophobic structure, CFn groups are inserted via C4F8 plasma treatment. After plasma treatment, contact angles of 160° and sliding angles of 5 ° were observed. This structure has also increased mechanical properties; when scratched, only the CFn groups that are on the top of the nanorods [parallel to NR axis] are destroyed; the low energy feature is thus preserved due to the CFn groups on the side of the NR. The structure as presented has average endurance to friction. Modifications should be applied in order to enhance tribological properties. Best results were observed for NR of 20μm length and 40μm diameter, regarding the hydrophobicity [167 ° contact angle, 5° sliding angle].
> Another method includes the use of graphitic nanofibers.Graphitic fibers are long, light and super-strong molecules that have been used in many applications requiring superb mechanical properties [mainly], light weight, and transparency. In combination with the current structure, at a low weight ratio [less than 10%]. The combined use will greatly enhance both the micro and nano roughness and the mechanical resistance of the protective film. Works on graphitic nanofibers [GNF] have proved their unique properties and their unlimited potential. This option should be especially studied, both experimentally and theoretically [first]. It is expected that all requirements of this project can be met without the need for additional plasma or heat treatment under severe conditions. Another advantage of GNF is that pre-treated GNFs could be used to further lower the coating surface energy. The chemical treatment of GNF is a well-researched field.
> An alternative composite could be created with the use of Graphene Sheets [GS] or modified Graphene Sheets [MGS]. The advantages of such a combination are numerous:
- Due to the work done in the last decade on GS, many options exist to increase its roughness and its surface energy
- GS are transparent with good mechanical properties
- Different GS preparation methods exist, covering this project’s requirements
- GS have demonstrated unique electronic and opto-electronic properties; thus they are a great fit for this project
- GS properties are tunable due to the easiness of insertion of functional groups
- GS roughness can also be tailored via creation of ‘defects’ and other accumulations of GS