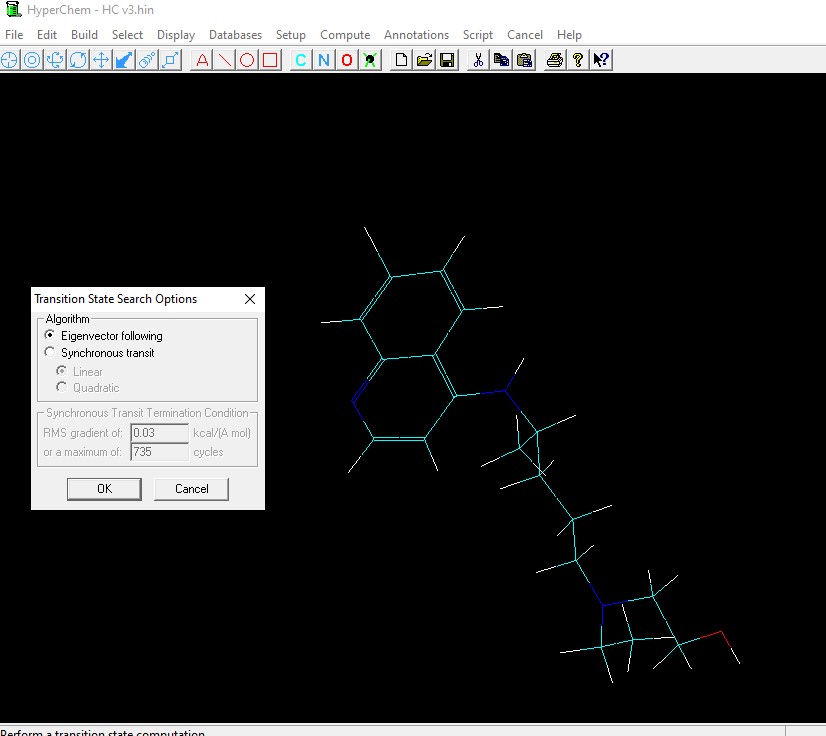
Artificial Intelligence and Machine Learning in Reaction Engineering
Reaction Engineering lies in the heart of Chemical Engineering and is an essential part of manufacturing processes where at least one chemical reaction takes place. When designing a chemical reactor several aspects are considered. Given a set of known reactants and reaction kinetics, one aims at producing a specific product. However, at large-scale, one has first to answer under which conditions (temperature, pressure and/or composition of reactants) the chemical reaction takes place, or to examine the potential of the production of byproducts.