Rapid color changing glass
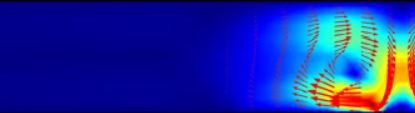
Our client has asked for the design of a new technology that allows for color changing glass for a specific commercial application [classified]. The project comprised of an initial investigation of all possible technologies for color changing materials and properties followed by a detailed investigation of the details of these technologies and their compatibility with the commercial product of interest. Such materials can fall under the following categories:
üThermochromic
üPiezochromic
üElectrochromic
üMechanochromic
üMicrofluidics
üLiquid crystals
üSuspended particles
üPhotochromic
üChemochromic
üSolvatochromic
The above material categories allow for optical properties change depending on the change of another factor. Temperature, pressure, electric voltage, stress, light intensity, pH, solvent type are only some of the factors of interest. The rate of change of such a property and the detection rate of this change govern the overall response time of the system. Known commercial applications commonly employ electrochromic materials when color change is the most important requirement, although other approaches have been used depending on the application. Liquid crystals is a very promising approach for accurate, demanding applications at micro scale due to atomistic scale orientation of atoms and molecules that they involve. Thermochromic materials have been utilized in applications where temperature control or display is required, as for example in heaters, building or reactor walls, even on the outside surface of coffee mugs. pH fluctuations are also monitored via color changing materials for military, health or irrigation purposes.
All the categories were evaluated against our requirements and design properties which included:
- Response time [ms]
- Number of colors plus transparent state
- Cost of manufacture
- Novelty
- Potential for a quick solution
- Required energy of operation
- Life of the product
Response time was very crucial for the specific application as it was the decisive factor for the user’s safety. We determined that the glass should have a response time for changing between transparent and colored phases in the range of 0.01- 0.1 sec. This response time is hard to achieve with some technologies, as for example with thermochromic materials that typically exhibit color changes in times ranging from some seconds to some minutes. Other technologies however meet this requirement. An additional design requirement was the ability to have at least three phases, whereas most current applications operate between two [transparent and colored]. This was proved to be feasible via at least three different approaches [classified]. Emergency operation [in case of battery down or malfunction] our glass should be able to operate for a few more seconds so that the user could safely terminate its use. Combination of all above requirements finally led us to the further examination of liquid crystals, microfluidics and electrochromic materials.
Mechanochromism/ Piezochromism was suggested as a potential solution for this project. This mechanism would require a force applied on two sides (or all around) a very thin film of an elastomeric polymer that would cause a strain [strains have been reported in the range of 2-300% for various mechanochromic films]. This strain is sufficient (for various films) to cause a change of optical properties and thus create a reversible transparent to opaque (or reverse) transitions. Several issues can be discussed at this point; for example, mechanical deformations do not exhibit the amount of reversible cycles that molecule orientation does. Another issue was the investigation of the required strain, keeping in mind the final application: if we achieve a 30% strain for our reversible transitions that would imply that adequate free space would exist on the lens to house this area increase? How? If the film is as thin as we plan to be, wouldn’t we need nanoscale mechanic locks in the sides for creating and maintaining of strain? Obviously, the thin film would be protected inside a group of layers that would provide hydrophobicity, anti-scratch, anti-thermal protection (among others). This also means that another condition has to be met in the interior of the device: zero friction between the mechanochromic and the next layer or no contact condition between them. Should any other condition be the case, friction would destroy the thin film upon strain and relaxation.
One partial solution to the above is the use of low strain mechanochromics, for example polymeric films containing carbon nanotubes or similar carbon allotropes. In this case due to the low strain required some of the problems mentioned above (such as the area generation) could be avoided. Also, mechanical properties are expected to be enhanced, although overall elasticity would be greatly damaged. Another issue however would be the increased cost and safety considerations.
Initially, piezochromic materials were also mentioned as a solution for the development of this tech. Piezochromic films would require a homogeneous force being applied on the whole surface of the piezochromic film by another film or a dense network of fibers (transparent, mechanically rigid, for example some kind of carbon fiber or carbon nanotube composite). In order to maintain the integrity of color or phase change of the film, this fiber network would have to be of micro/ nano scale so that the naked eye would not catch the ‘voids’ created in the surface. In any case, this would be feasible but more manufacturing steps are included. The interaction between the pressure network (fibers) and the piezochromic film would also need investigation and modification since the motion of the two entities should be synchronized to eliminate high pressure and crack regions (that would lead to lower quality of uniform optical change and mechanical degradation, respectively). No matter the above disadvantages, piezochromic materials seem like a more feasible choice than mechanochromic materials. Power consumption should be higher than that required by mechanochromic approach. Estimation of power consumption is also feasible once the piezochromic film’s identity is known. Mechanical deformation repeatability is higher than in the mechanochromic case but lower than in the orientation case.
In a latter phase, CFD simulations were employed as to design the microfluidics network that would meet our requirements for the manufacturing of the commercial product. Flow rates, pumps, pressures, fluid properties, channel material and network, energy consumption were all calculated for different microfluidics designs until we reached an optimum state. That state was sent of to a manufacturing lab for prototype design via 3D printing using the transparent polymer [classified] with the minimum pressure drop and longest life. At the same time, a novel multilayer electrochromic was also designed based on CFD simulations. Liquid Crystals approach is at a hold due to the great progress in the other two fronts. Successful manufacturing of the microfluidics prototype will lead to the launch of the product in the next couple of years.